Using the SCM to control coagulant dosage
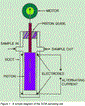
By Robert L. Bryant
The most critical time in the water-treatment process usually occurs within the first two minutes of the raw water's entering the plant. What the operator does, or does not do, in this short time span affects everything in the system. Enter the streaming-current monitor.
The results of coagulation control problems are well known and includes poor finished-water quality, high chemical costs, short filter runs and high backwash costs, excessive sludge, increased pumping costs (raw and finished), and post precipitation.
Every water-plant operator's goal is to maintain good finished-water quality, which in large measure depends on the operator's maintaining proper coagulant dosage. Jar tests, pilot filters, and zeta meters are some of the methods used to determine the required feed rates, but each has inherent drawbacks (such as not offering real-time results).
Experienced operators have learned to cope with such factors as changing raw water turbidities and flow swings, but there are times when it is beyond their control to react quickly enough to maintain desired water quality. (In sludge dewatering applications (belt presses, centrifuges, and so on), sludge concentrations can change rapidly, resulting in frequent conditions of overdosing and under dosing.)
The general tendency in a water or wastewater plant, therefore, is to overfeed chemicals as a "safety" measure. This overfeed may range from 10% to 50%, or more.
Streaming-current Monitor:
The Streaming Current Monitor (SCM) is a continuous sampling, online instrument that enables the treatment-plant operator to know precisely, and at all times, the optimum coagulant dosage. The SCM responds to changes in raw- water characteristics (turbidity, pH, color, etc.) and flow rates, and allows the operator to make the necessary adjustments. It also provides an immediate alarm if chemical feed is interrupted for any reason. The SCM works equally well with inorganic coagulants (alum, ferric com-pounds) and all polymers that possess positive or negative charge.
The SCM is a charge-measuring device. The charge measured is the net ionic and colloidal surface charge (positive and negative) in the sample being tested.
Streaming current* is a measurable electric current that generates when particles in water are temporarily immobilized, and the bulk liquid is forced to flow past the particles. Since the amount of current generated is proportional to the charge remaining after coagulants have been added, it is the algebraic sum of the currents generated, and therefore much less subjective than zeta potential measurements. Since the SCM samples continuously, operator error in sampling or testing is eliminated.
Figure 1 is a simple diagram of the sampling cell. The treated sample flows into the chamber where it is drawn into the bore during the piston upstroke and is expelled on the down stroke. Particles in the sample are temporarily immobilized on the piston and cylinder surfaces. As the water is moved back and forth, mobile counter ions surrounding these particles are moved downstream to the electrodes. This reciprocating movement of like charges causes the generation of an alternating current, which is defined as the "streaming current." This current is amplified through the appropriate electronics and displayed on a recorder, meter, or both.
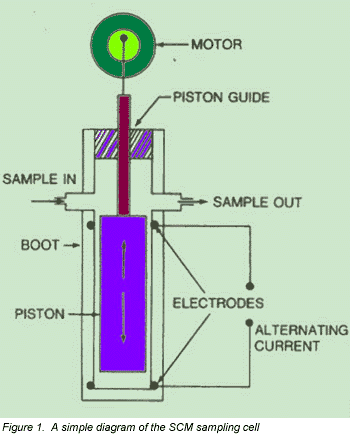
Figure 2 shows how the SCM fits into the treatment scheme of a water plant. The unit works in direct filtration plants as well as the conventional process shown. The sample must be taken at a point where uniform distribution and mixing of coagulant is obtained for all flow rates. If uniform distribution and mixing is not obtained at a selected sample point, the SCM reading will oscillate.
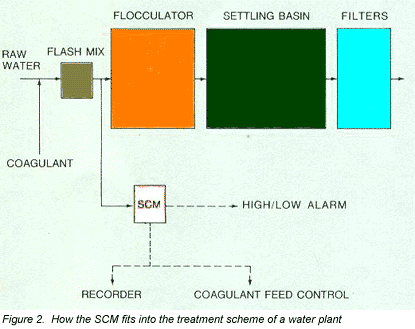
The Benefits of SCM
Coagulant control. The SCM produces a 4- to 20-ma signal that can be used to automatically control the coagulant feed. To optimize the system, the operator simply adjusts coagulant dosage and observes the reading on the SCM corresponds with the lowest feed rate that produces acceptable water quality. This is the "set point," which will remain very close to the same value during periods of high raw-water turbidity. The operator has only to adjust coagulant feed to maintain this value.
The SCM also has contacts for high and low alarms that can be set to alert the operator to treatment upset.
System-analysis capability. By being able to continuously measure the net electrokinetic charge at any point in the system, the SCM allows operators to see such effects as produced by erratic chemical feeders, variations in alum content, chemical mixing and distribution problems, and short circuiting.
Aluminum carry-through prevention. Aluminum can enter the finished process water as a result of poor coagulation, alum overfeed, or poor pH control in the flash mix. This is especially true for raw waters with low alkalinity where lime or caustic is used to adjust pH at the point of initial coagulation. Alum has a fairly wide pH range in which good flocculation and settling occurs. However, there is a specific pH at which the minimum amount of aluminum will carry through the filters. Even a small overdose of 1 to 2 mg/L can significantly increase aluminum carry through.
The detrimental effects of post precipitation have been known for years. Aluminum hydroxide can deposit on any type of pipe lining. Even a thin coating will reduce water throughput capacity and increase pumping costs. Deposits in lines accelerate corrosion mechanisms—and can even contribute to microbiological growth. Corrosion-control programs using phosphates and/or zinc are adversely affected by aluminum carry through. Feed rates of these inhibitors must be increased to maintain desired corrosion protection.
Plants have found significant reductions in finished-water aluminum following the placing of the SCM into service—allowing the alum dosage to be minimized.
Reasons for SCM Restated
The SCM generally has been chosen as the coagulation control system where it has been evaluated alongside pilot filters, and zeta meters for the following reasons. It
- continuously generates a signal that shows the operators whether they are overdosing or under dosing;
- does not require backwash, media replacement, or calibration;
- performs accurately and reliably at all turbidity levels normally encountered in water and wastewater;
- can be used to automatically control coagulant feed using the signal it generates; and
- can minimize plant upsets via its high and low chemical-feed alarms.
Contact: Chemtrac Systems, Inc., Bldg. 600, 6991 Peachtree Industrial Blvd., Norcross, GA 30093. Tel: 770-449-6233, 800-442-8722; Fax: 770-447-0889
*Streaming current is related to zeta potential by the formula I = (kZD)/N; where i = streaming current, Z = zeta potential, D = dielectric constant, k is a proportionality constant, and N = viscosity of the fluid. Zeta potential is a measure of the stability of a colloidal dispersion. Zeta meters generally provide a more precise measurement for determining correct dosages than jar tests or pilot filters. However, this is a non-continuous sampling method, and requires good laboratory techniques to do it properly.
About the author: Robert L. Bryant is president of Chemtrac Systems, Inc.
The previous article was adapted from the article, "Water treatment control using the streaming current monitor," written by the author for distribution as a company information circular.