Shocks no Solution to Stuck Hoppers
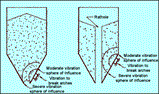
Solving hopper hang-ups can involve brute force, vibration, air lances, shakers, air cannons, vibrated (activated) hoppers, or just plain cussing. The results often are less—and more—than sought.
Brute force hardly produces lasting cures—as evidenced by the "hopper rash" (sledge-hammer pockmarks on hoppers and chutes), which often deteriorates into fully "malletized" hoppers that no longer have their original cone or pyramid shape.
Air lances and cannons create sudden collapses that fluidize powders, making even the slightest crack a nozzle for fluidized solids. Vibrators and shakers placed on ordinary hoppers often split welds and create ear-splitting noise. The severe impact of falling solids shaken loose by the vibrators and air cannons often results in worse compacting of the hopper's content. In extreme cases, the impact breaks welds and tears hoppers from their upper vertical bin sections.
Vibration's Failings Explained
Vibrated (activated) hoppers, suspended to allow the entire hopper to vibrate on hanging supports, seldom give uniform flow across their entire top diameter. This leaves one-half to three-quarters of the material above the bin activator inactive. If the level is maintained within the bin, these inactive regions may harden into solid blocks that either remain an integral part of the structure or dislodge to block the outlet or annular region around the inside baffle of the activated hopper.
When a full bin (the upper vertical section) or hopper (lower converging section) is vibrated, the solids contact pressure increases, and the bulk solid compacts and becomes less likely to flow.
For vibration to be effective its influence must reach a stress-free, or unconfined surface, such as an unsupported arch or rathole (see figure).
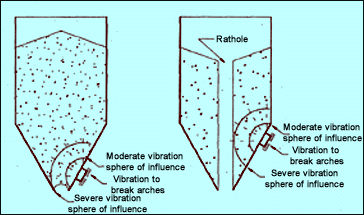
Ratholes are vertical wells in hoppers and bins that extend vertically above the hopper outlet or above a flow channel created in a hopper. Essentially, ratholes are horizontal arches that derive integrity from a continuous horizontal hoop stress. Any conical or pyramidal hopper that does not have flow at its walls will form a rathole. If the bulk solid is slightly cohesive, the rathole will be stable.
The vibration, by increasing the stress acting along the stress-free surface, may overcome the resistance of the compacted material, initiating flow.
However, unless the vibration reaches the solid's stress-free surface, rather than freeing the material, it induces further compaction. The over-compaction often requires more forceful and sustained bin vibration to initiate flow, creating a self-perpetuating, destructive cycle.
Also, the cycle of compaction and failure can repeat if the vibration continues after flow starts. Vibration applied to a material like wood chips, sawdust, chopped fiberglass, metal turnings, or other springy-type solids almost always has this outcome.
The vibration's sphere of influence depends on vibration strength, hopper geometry, hopper reinforcement details, solids flow properties, the level of solids in the bin, and how the solids were loaded. This makes vibrator selection and placement more art than science and therefore, very error-prone.
The better solution to these problems lies in the passive activation concept that uses unique bin shapes to concentrate enough energy to break ratholes and arches.
Passive Activation
The potential energy available from gravitational forces on the stored solids in a bin is simply the weight of the solids multiplied by the height of the bin through which it moves. This energy dissipates during deforming of the solids (internal friction), and by frictional energy at the bin walls (surface friction.). Therefore the design of the bin and hopper must be such that, when solids flow, sufficient energy must remain to break the cohesive forces that would otherwise cause hang-ups.
Passive activation occurs when properly shaped bins and hoppers conserve the potential energy of the contained bulk solid and gently concentrate this energy to keep arches (obstructions on a bin's side walls) from forming and provide a first-in, first-out flow sequence from the bin.
First-in, first-out flow in bins and hoppers causes a remixing at the hopper outlet of previously segregated material in the horizontal bin's cross sections. Typically this means combining a conical hopper steep enough to cause flow at the walls with a tall vertical section, while maintaining a head of solids one-half a diameter above the hopper or higher. If the cone empties, some segregation will result.
Vertical Bins Walls. Successful passive activation occurs when the hopper's shape minimizes energy dissipation as the solid moves through the bin. Generally, this means reducing the internal deformation and energy lost to internal friction.
The least energy dissipation occurs in a vertical-wall bin with no convergence. In this case, the only energy dissipated internally is that associated with changes in the solid's bulk density. Unfortunately, this bin design requires an expensive, live-bottom, multiple-screw feeder equal to the bin's cross section.
Also, feeders of this design require excessive power to dissipate the solid's potential energy during the feeding process. Although feeders designed for extra capacity in the direction of feed make arching and ratholing within the bin virtually impossible, if even a short section of the screw's discharge prohibits solids to in feed, severe compaction occurs and arching is inevitable even with slightly cohesive solids.
Conical Hoppers. The most extreme case of internal energy dissipation occurs in a conical hopper with flow at the walls. The multi-directional convergence of a conical flow channel is very effective in dissipating energy internally. Flow at the converging walls of a hopper will occur only if there is sufficient potential energy in a given volume of solids to satisfy both the internal-energy dissipation and the wall-friction-energy dissipation. The frictional energy loss from the flowing solids against the stationary solids dissipates the remaining potential energy so that little is left to break hang-ups at the hopper outlet. When solids reach the hopper outlet, there may be no energy left to break bridges and eliminate hang-ups.
As a hopper's walls flatten, the available potential energy for a given volume decreases until flow no longer occurs at the hopper's walls but is confined to a smaller limited flow channel above the hopper outlet.
This limited flow channel restricts energy dissipation to an almost vertical channel's having little or no convergence, and reduces the stress on the flowing solids. As a result, hang-ups are even more likely in a conical hopper with walls that are insufficiently steep to cause flow at the walls than in a conical hopper with flow at the walls. *
* The author has overcome the deficiencies associated with some passive activation designs with the patented energy-conserving Diamondback Hopper.
The previous article was motivated by and adapted from, with additions, the article "Economical Passive Activation Solves Bin Hang-ups," which was edited by Angelo DePalma for Pharmaceutical Online, a sister site to Pollution Online within the VerticalNet e-commerce family.
About the Author: Jerry R. Johanson, PhD, is president and CEO of Diamondback Technology by JR Johanson, Inc. 1237 Archer St., San Luis Obispo, CA 93401. Tel: 805-783-4484.