Reducing Furniture Industry Emissions
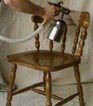
The wood-furniture and fixtures industries' coating usage accounts for about 15% of all product finishes (not including architectural or special-purpose coatings) consumed by industry.
More than 10,000 wood-furniture-manufacturing facilities operate in the U.S., consisting mainly of small companies. Their exhaust streams constitute a high volumetric flow and low VOC concentration due to the large volume of fresh air usually used in manual spray operations.
Because the majority of the solvents consumed by the wood-furniture and fixtures industries are VOCs, solvent usage is approximately equal to VOC emissions.
Wood-furniture-industry Emissions
VOC/HAP emissions in the wood-furniture industry comprise many sources. They include such operations as finishing (spray booths, flash-off areas, ovens), cleaning, mixing, touch-up and repair, and gluing.
Finishing operations typically account for the largest portion of facility-wide VOC emissions. Typical pollutants emitted include alcohols, methyl ethyl ketone (MEK), methyl isobutyl ketone (MIBK), toluene, and xylene. Acetone, although not considered a VOC, also is emitted by the industry in large quantities.
One or more of several designs of spray guns usually are used to apply finishing materials in booths.
Application may be manual or automatic, but the majority of spray booths operate using manual finishing techniques. (Most spray booths incorporate dry filters to control particulate (paint droplets) generated by overspray.)
Finishes also may be applied using techniques such as roller, curtain, and dip coating.
Cleaning operations generate emissions of VOC/HAP where an organic solvent is used to clean application equipment, spray booths, or other equipment.
Organic solvent generally is needed to clean equipment that has been used to apply solvent-based and UV-cured coatings, while hot water may be used to clean equipment used to apply water-based coatings.
Cleaning of spray guns, where required, usually is done by sending solvent or water through the gun and atomizing the liquid into the booth ventilation system.
Some VOC emissions may occur during mixing operations if volatile materials, such as thinning solvent, are used or if material is spilled. Touch-up and repair operations are a source of VOC emissions if solvent is used to strip a piece of furniture or perform spot rework.
Gluing operations can potentially be as large a source of emissions as finishing operations, depending on the type of glue used. In the past, glues containing methylene chloride were widely used and could account for a significant portion of a facility's HAP emissions. In recent years, wood-furniture plants have transitioned to water-based, hot-melt, or low-VOC/HAP adhesives as alternatives.
Pollution Prevention in the Wood-furniture Industry
Pollution prevention is the use of materials, processes, or practices that reduce or eliminate pollution or wastes at the source. Also called source reduction, it includes practices that reduce the use of hazardous materials, energy, water, and other resources. Thus, instead of controlling pollution with an add-on control device, the facility, for instance, institutes work practices that prevent or reduce the pollution from being generated.
In addition to any emissions reductions achieved, pollution-prevention practices also can serve to reduce operating costs, reduce permit fees, reduce liability and fire risk, improve employee morale, and enhance a company's image.
Typical Industry Pollution-prevention Practices
Because the quantity of VOC emitted is directly related to the amount of coating used, common pollution-prevention measures involve reformulation of the coatings and glues. Reformulation to higher-solids or water-based coatings by reducing the amount of solvent in the coating (and possibly) the volume of coating required per piece, should reduce VOC emissions. Converting to UV-cured or powder coatings will further serve to reduce volatile emissions. However, implementing these types of coatings and their associated application equipment is not always cost-effective, especially for small companies.
Simple housekeeping measures, such as keeping containers of coating covered and minimizing spills, also serve to reduce VOC emissions. Recycling cleaning solvent will cut down on cleaning emissions, as will reformulation of cleaning solvent. Using coating supply lines and spray guns dedicated to particular coatings and colors will also reduce cleaning emissions because lines will not need to be flushed when a different color of finish must be applied. Depending on the types of materials used, coating and gluing materials also can be recycled.
Use of more efficient application equipment, such as HVLP spray guns, automatic spray, or flat line finishing, will serve to reduce emissions associated with coating overspray (more coating is applied onto the piece). However, to ensure that the operators are using the equipment correctly, an operator-training program should be implemented. Operators should be instructed in proper application technique and appropriate equipment settings, such as pressure.
Other pollution-prevention options exist for reducing facility-wide waste and emissions, including recycling programs for waste wood, packing materials, and empty containers. The laundering of cleaning or wiping rags—if free from solvent—instead of disposing of them after one use, also is a means of reducing waste. Use of more efficient application equipment also will produce less waste (because booth filters need change less often) and require less coating.
What Experience has taught
Although most surface coating regulations require facilities to use finishes with low VOC or HAP contents, some in the industry have been concerned about having to move away from conventional, solvent-borne, nitrocellulose-based finishes that have been used for many years. One reason is because many furniture companies that tried water-based coatings in their early stages of development found that they did not perform as well as solvent-borne coatings. Specifically, there were problems related to appearance, grain raise, and dry time. In addition, conversion to UV-cured systems is often viewed as capital intensive.
To address these concerns, Midwest Research Institute and the U.S. EPA initiated a cooperative agreement to find facilities that were using low-emitting coatings successfully and to provide information on their experiences to the industry. The types of case studies completed and the typical issues associated with the use of water-based, UV-cured, and powder coatings are covered in the presentation from which this article derived.
About the authors: Amy M. Marshall and Jennifer L. Spaight are with the Midwest Research Institute, 5520 Dillard Rd., Suite 100, Cary, NC 27511. Julian W. Jones is with the U.S. Environmental Protection Agency, Air Pollution Prevention and Control Division (MD-61), Research Triangle Park, NC 27711
This article was adapted from paper 99-161, "Pollution Prevention and the Use of Low-VOC/HAP Coatings at Wood Furniture Manufacturing Facilities," prepared for presentation at the Air & Waste Management Association's 92nd Annual Meeting & Exhibition, June 20-24, St. Louis, MO.