Primer on stack-emissions testing — Part 4: Critical support requirements
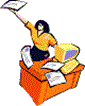
The issues to be considered for site support are sampling ports, scaffolding, operator support, coordination with regulators, and safety.
Confirming the validity of the data
Site support
Scope of work
Conclusions
Parts 1 to 3 of this article reviewed the basics of stack-sampling methods and their procedures, providing information helpful to planning a stack test and obtaining reliable data. Here, before tackling the main thesis of this concluding section, we first conclude the topic of testing being discussed in Part 3.
Confirming the validity of the data
Sample recovery/analysis. Sample recovery and sample control are vital elements of stack sampling. Samples must be recovered as prescribed by the selected test method, and the sample must be properly identified.
Since samples usually are analyzed well after site work is complete, any mistakes at this point guarantee costly retesting. Close communication between the test officer and the lab is necessary to ensure that the analytical results are properly understood and appropriate supporting documentation provided to regulators.
A well-organized sample-numbering scheme must be established prior to testing. Sample numbers and sample identification for identifying run number, matrix (filter, probe wash, resin, etc.), spikes, and blanks must be recorded to ensure against confusion after analytical results are received.
Most target compounds have a maximum allowable holding time before analysis must be completed. Samples thus may have to be preserved prior to shipping to the analytical lab. This usually translates into icing down the samples or adding a preservative. Keeping track of this information is the sample coordinator's job. The samples also must be properly packaged to ensure against damage during transport and that preservation efforts will be effective.
Finally, samples must be under a proper chain of custody. This is particularly important for compliance testing.
Other than to note the need for proper analysis of samples with supporting QA data and equipment calibration data, commenting on the actual analysis of samples is beyond the scope of this article.
Test documentation. After the analytical results are available, the test officer has all the information necessary to complete calculations and to prepare a report. The data needed for this are facility operating data, sample-train-calibration and -operating data, and analytical data. Report content will depend greatly regulator requirements. A suggested format is given in Figure 1.
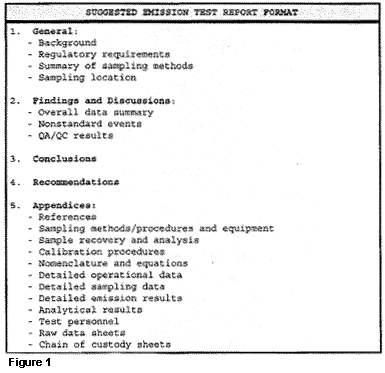
If all parties agree, a less comprehensive report may be acceptable. In some cases, a preliminary report providing data only may suffice to initiate permitting by the regulators. This can be followed up later with a more comprehensive report. The author's experience indicates that more is better and that the incremental time necessary to prepare a detailed report is worth the investment.
One issue that frequently arises is the need to provide raw data sheets to the regulators. Occasionally, regulators will require a copy of the data sheets immediately upon completion of testing. More likely it will be possible to include the raw data as an appendix to the test report or to submit the data under separate cover. In lieu of other guidance, minimum report requirements comprise:
For a successful test, issues like sampling ports, scaffolding, operator support, coordination with regulators, and safety must be considered.
Sampling ports -- Unfortunately, it is not uncommon for sample ports to have been overlooked during design and construction or improperly located. The time to locate sampling ports for a new facility is during the design phase. Sample ports must be located away from both downstream and upstream flow disturbances such as fans, dampers, elbows, and the top of the stack. Sample ports preferably should have a 4-in inside diameter. Metal screw-on caps should be provided.
Existing facilities that have previously been stack-tested will probably have adequate sample ports. The tester, however, should verify this, during the preliminary survey.
Adding ports may be necessary where emission-test requirements have changed since the last stack test. Also, three or more trains on complex tests are not unusual, requiring additional sets of sample ports. This is a relatively simple undertaking that can be done with installation assets or by contracting. The primary skill involved will generally be welding.
Most test organizations are not prepared to install sample ports. So the test organization should advise the installation accordingly.
Scaffolding -- Access to the sampling site frequently requires the construction of scaffolding. The scaffolding should support a platform of sufficient size and strength to accommodate the testers and equipment needed in the immediate area of the sampling ports.
As with sample ports, scaffolding should be a design consideration. There is an economic issue here: A facility such as a boiler plant or incinerator that will be tested repeatedly may justify permanent scaffolding.
The scaffolding and access ladders should meet OSHA standards and the installation safety office should approve it. Temporary scaffolding is perfectly acceptable when properly constructed. Many stack tests have been conducted out of man lifts (cherry pickers). This practice is not recommended: It is difficult to install the sampling equipment and is not conducive to the level of concentration that is necessary to properly operate the sampling equipment at the stack. In addition, the practice is time consuming and will frequently require a separate operator to manipulate the lift compartment.
Also, safety is a concern from the point of view of dropping test equipment and tools while operating under awkward circumstances. Still, most stack testers are very reluctant to be the cause for a test delay and probably take more chances than they should. The installation should avoid putting the team under this pressure.
Stack testers do not usually provide scaffolding, so this requirement will fall to the installation. The stack tester can provide design information such as weight support requirements, platform area, height below sampling port, and orientation.
Operator support -- Successful testing, as previously mentioned, is keyed to operator support. A test will be invalid if desired operating conditions are not maintained during the test. A very basic example would be the feed rate to an incinerator during the test. A low feed rate during testing will result in a permit with low allowable feed rates. Also since three runs must be conducted at each operating condition, significant fluctuation in the feed rate from run to run could also result in invalid data or a low allowable feed rate.
Moreover, for complex testing such as RCRA trial burns, volumes of data must be collected. This is not a trivial task and requires an operator who knows and understands the data acquisition system of the facility. This issue needs to be resolved in the protocol, and an operator should be designated to obtain that information.
Coordination with regulators -- Compliance tests will almost always involve direct discussions with regulators. Testers should be willing to assist the installation in resolving such test requirements as applicable standards and methods. Still, the initial contact and development of points of contact should be done by the installation. Most environmental staffs maintain close working relationships with regulators, and this should be a fairly simple task.
Safety -- The test organization certainly has the basic responsibility for safety of its personnel. In addition to the safety concerns previously discussed for scaffolding, other concerns involve exposure of the test team to the elements; exposure to heat from breechings and ducts; exposure to stack gases; falling objects; and and noise.
Stack testers should be prepared to work under arduous weather conditions through use of proper clothing and rotation of exposed workers. Since stack testing involves operating electrical equipment, testing should never be permitted during rain without suitable overhead protection. Also, the installation should be cognizant of safety concerns and assist the test team anyway possible. Again, pressure to complete testing should not be a reason to relax safe practices.
Miscellaneous -- Other requirements that may surface include, but are not limited to:
Figure 2 includes a list of elements that should be addressed in a solicitation scope of work. Be prepared to closely investigate the proposal in detail to be assured that your requirements will be fulfilled. Have a clear understanding of the cost implications if the test does not go off on schedule. Make sure you are getting a commitment to test for the pollutants of concern using approved methods.
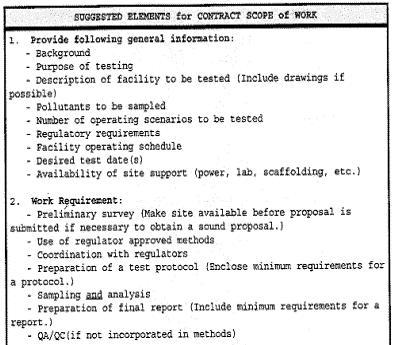
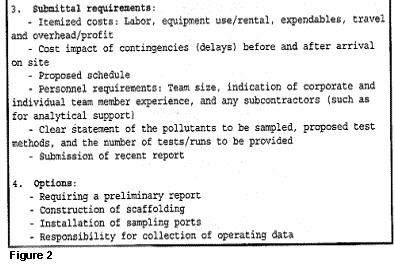
(Back to top)
Stack testing can be a complex undertaking that requires extensive preparation and a competent test team. A basic understanding of stack test methods, a complete scope of work for test services, and support during the testing will ensure a successful test.
About the author: David L. Daughdrill is program manager, Air Pollution Source Management, U.S. Army Center for Health Promotion and Preventive Medicine, Aberdeen Proving Ground Edgewood Area, Maryland. Tel: 1-800-222-9698. (Back)