Plasma arc centrifugal-treatment process matures
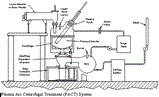
By: Retech Services Inc.
Plasma-arc centrifugal-treatment vitrification technology has advanced from the first experiments in 1985 to occupy a niche in the waste-treatment market. The components of the system work together to achieve high organic removal efficiency and generate a durable, homogenous, vitrified waste.
A plasma-arc centrifugal-treatment (PACT) system achieves vitrification by transferring heat from a plasma-arc torch to create a molten bath.
In operation, waste material feeds into a sealed centrifuge, where a plasma torch (created by ionizing nitrogen in a hot gas stream) heats solids to approximately 3200°F and gas headspace to a minimum of 1800°F.
Solids melt into the molten bath. Organic material is evaporated and destroyed. Off-gases travel through a gas-slag separation chamber to a secondary chamber, achieving a temperature of more than 2000°F for at least 2 seconds. The off-gases then flow through an off-gas treatment system.
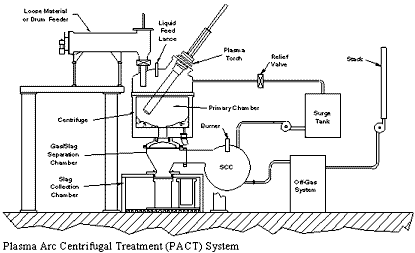
Inorganic material reduces to a molten phase, being uniformly heated and mixed by the centrifuge and the plasma arc. Material can be added in process to control slag quality. When the centrifuge slows, the molten material is discharged as a homogeneous, non-leachable, glassy slag into a mold or drum in the slag collection chamber. When cooled, the resulting product is a non-leachable, glassy residue that meets toxicity characteristic leaching procedure (TCLP) criteria.
Because of the very high plasma temperatures, it is possible for relatively high concentrations of metals from the waste to vaporize. There thus is a need to capture these vapors using the air-pollution-control equipment that can capture sub-micron sized particles. Because of localized reducing conditions around the plasma arc, soot generation may occur as well.
Off-gas monitoring verifies that all applicable environmental regulations can be met. The design of the off-gas treatment system depends on the waste material.
The entire system is hermetically sealed and operated below atmospheric pressure to prevent leakage of process gases. Pressure-relief valves connected to a closed surge tank open if gas pressure in the system exceeds safe levels. Vented gas is held in the tank, then recycled through the PACT system.
Building a Base
Several PACT units—comprising -2, -6, and -8 units, both pilot and commercial—are in operation in Europe and the USA.
The unit with the longest operational history is a PACT-8 pilot system at the Moser Glacer & Company (MCG) in Switzerland. It has been treating low-level radioactive wastes since about 1990. Initially used for research and demonstration purposes, it has been operating commercially since 1996.
A contract is underway with Toyo Engineering Company of Japan for the Tsuruga nuclear power plant. This system is scheduled for shipping mid-year 2000. It is designed to feed 200-L drums, both horizontally and vertically, and loose organic waste.
Another PACT-8 system—designed and built for the pending remediation of Pit 9 at the Idaho National Engineering Laboratory (INEL)—embodies a 1500-kW plasma torch.
The air-pollution control system for the Pit 9 system is designed for the capture of radioactive metals, other particulates, soot, hydrogen chloride, and sulfur dioxide. The system design includes a cyclone, spray quench tower, packed bed absorber, a Hydrosonics scrubber, a chiller to cool the gas to 105ºF for mercury removal, cyclone and mesh mist eliminators, a flue-gas reheater, prefilters, and HEPA filters.
Improvements on the Horizon
Currently, the combustible organic content of the waste is the limiting parameter on throughput based on combustion-gas flow-rate limitations to the air-pollution control system.
Modeling based on data indicates that the full-scale, PACT-8 unit is capable of a throughput of 1558 lbs/hr of waste feed at 23% organic content. Possible throughput enhancements may result in waste feed rates for the PACT-8 of more than 2000 lbs/hr and an operational availability of 80%, compared with the 43% availability of units now in operation.
The previous article is a synthesis of material adapted from several papers prepared by Retech Services Inc. Retech is a wholly owned subsidiary of Lockheed Martin Corporation.
Contact: Retech Services Inc., R.K. Womack, PO Box 997, 100 Henry Sta. Rd, Ukiah, CA 95482-0000. Tel: 707-467-1721; Fax: 707-467-1638; or U.S. EPA, Laurel Staley, National Risk Management Research Laboratory, 26 West Martin Luther King Drive, Cincinnati, OH 45268. Tel: 513-569-7863; Fax: 513-569-7620.