Meeting the food-processing industry's new MACT requirements — Part 2
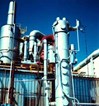
Part 2 of this article covers the attributes and shortcomings of some of the pollution-control equipment available to the food industry to meet Maximum Achievable Control Technology (MACT) requirements. (Click here to read Part 1.)
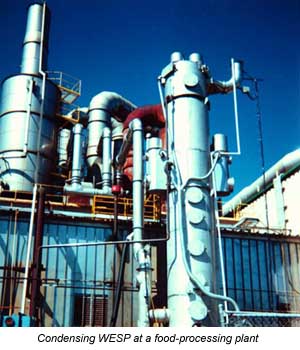
MACT requirement for eliminating VOCs from food-processing-plant stacks are a looming challenge for the industry. So then is the appropriate selection of equipment to meet the standards.
Rating the Air-pollution-control Candidates
Fiber filters or fiber-bed mist eliminators seldom commend themselves to food-processing applications. The high flammability of VOCs in the gas stream, the probability of plugging, and the expense of filter disposal usually preclude the use of dry-filtration devices.
Wet scrubbers—as do fiber filters—use impaction, interception, and diffusion for collection. The important difference is that a scrubbing liquid rather than fibers perform the filtering role, removing the potential for fire or explosion. Wet scrubbers often are employed for removing large particulate matter and odor-causing non-condensable organics from a gas stream. However, they cannot handle VOC smoke abatement.
Condensed VOC droplets typically are smaller than one micron. To collect them from the exhaust gas stream, the optimum target droplets must be in the range of 10 to 15 microns—much smaller than the drops generated in the simple wet scrubber.
The high-energy Venturi scrubber is a gas-atomizing device relying on sheer and impact forces to break the water into an evenly distributed cloud of very fine droplets at high density. This method of VOC abatement is relatively effective but costly to operate because high pressure losses result in high energy requirements to operate the system.
Packed-bed wet scrubbers and scrubber/quenchers provide intimate contact between scrubbing liquid and odor-producing gas. Substantial odor reduction occurs through the mass-transfer capability of the packing that is flooded with scrubbing liquid. This equipment can be useful in situations requiring ancillary odor abatement. It does not, however, eliminate the blue-smoke problem.
Activated carbon adsorbers have deep beds of carbon
They thus effectively eliminate VOCs, fumes, and odors in moderate-volume applications. Most frequently they find use in concert with electrostatic precipitators and other gas-scrubbing equipment in high-volume systems.
Electrostatic precipitators are particularly effective at removing the sub-micron particles that create blue smoke and odor.
(For a synopsis of the above discussion of equipment properties, see Table 1 below.)
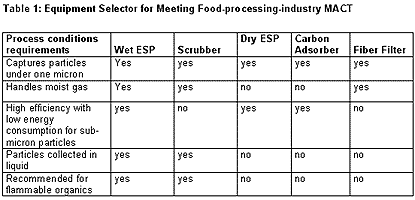
Electrostatic Precipitation
The electric force exerted on an electrically charged particle of 0.1 micron can be more than one-million times the force of gravity on that particle.
Electrostatic precipitators (ESPs) employ electrical forces to remove suspended particles from the gas stream. Three steps are involved in electrostatic precipitation: charging, collection, and removal. A corona discharge between negative and positive electrodes electrically charges the suspended particles. The corona power of an electrostatic precipitator is the product of the operating voltage and the operating corona current.
Because an ESP uses electricity only to charge particles without restricting the air stream, it requires ten times less energy than does a Venturi scrubber for comparable efficiency of smoke removal.
Electrostatic precipitation often can be the optimum filtering choice, since tiny particles usually respond well to electrical forces. So where aerosol droplets of VOCs are a concern, electrostatic separation often follows the scrubber stage in the air-pollution-control system for a food-processing-plant exhaust gas.
The charged particles from the electrostatic precipitator collect on electrodes.
Removal Strategies Vary
In a dry electrostatic precipitator (ESP), the electrodes are shaken periodically to remove accumulated particles for disposal. Despite that shaking, dry ESPs are prone to particle buildup on the walls of the collection chamber. The buildup acts as insulation, reducing the overall efficiency of the equipment.
Dry ESPs can be used alone for the removal of dry particulates that are not sticky, but must be combined with scrubbers or similar equipment to capture VOCs.
In a wet electrostatic precipitator (WESP), a liquid, usually water, continuously washes particle buildup from the collection surface. The WESP widely is used for applications where the gas to be treated is hot, has a high moisture content, and contains sticky particles or sub-micron particles that cannot be treated by other methods—situations typical of food-processing-industry conditions.
In most cases the gas is pretreated in a scrubber situated at the bottom of the WESP. The WESP provides complete particulate removal with a high level of efficiency.
In a conventional "upflow" WESP the gas stream flows co-current to the water spray. This requires frequent cleaning because bottom water sprays are not completely effective in reaching the top of the chamber where sub-micron particles accumulate. The "down-flow" WESP overcomes these problems but does require mist elimination following treatment.
The condensing, vertical-tube WESP increases removal efficiency, especially of sub-micron-size particles, and reduces operating costs and maintenance by harnessing temperature to create particle movement perpendicular to the direction of the gas flow.
The design combines a quencher to cool the gas stream with an up-flow, vertical-tube WESP. It integrates variables of velocity, particle size, and temperature to maximize removal of sub-micron particles.
In addition, by condensing out the water vapor from the contaminated gas, the condensing WESP design greatly reduces the amount of makeup water. The continuous presence of condensate also reduces the potential for corrosion.
Typical Treatment Train
In a typical WESP application, the hot, contaminated inlet stream is cooled from 300 ºF to 140 ºF in a quencher. Then a low-energy scrubber removes particles larger than 2 microns.
The pretreated gas stream passes into a series of tubes containing ionizing electrodes. Each electrode has a number of sharp points that provides the corona discharge. When the particles are charged to the point of saturation, they migrate toward the walls of the collecting tubes.
Within the double-walled collection chamber processes take place that impart additional energy to the particles and greatly increase the effectiveness of the device. They are
Optimum, Integrated Approach
In the food processing industry, the Condensing WESP possibly is the optimum single selection for air-pollution abatement. The combination of liquid scrubbing, thermophoretic, and diffusiophoretic effects—plus high-voltage electrostatic precipitation—is an effective method for sub-micron-particle removal.
The WESP is also an excellent candidate for operation as part of an energy-efficient, low-maintenance integrated system. By preceding a WESP with a low-energy scrubber—designed to act as the air-distribution device and odor abatement section—and following it with an activated carbon adsorber to treat non-condensable, low-molecular-weight organics, both blue smoke particulate and odor problems are effectively abated.
The Condensing WESP is a MACT solution for keeping food-processing plants in environmental compliance.
About the author: Isaac Ray, PhD, is a principal with Croll-Reynolds Clean Air Technologies, Westfield, NJ. (Back to top)