Large Machinery/Plating Operation Recovers its Wastewater
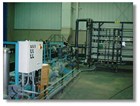
One of the facilities manufactures components with metal machining and finishing operations.
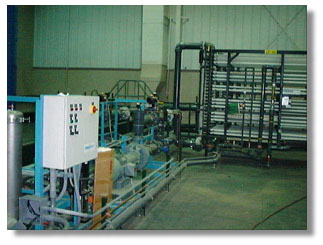
The control center of the wastewater recovery system
Problem:
The manufacturing of the metal parts results in several aqueous waste streams containing metal contaminants, including boron, chrome, iron, and zinc. The waste streams also contain a variety of other chemicals including sulfuric acid, hydrochloric acid, potassium hydroxide, oils, synthetic coolants, and surfactants.
The company had to confront the question of how to best capture reusable product, including water and dissolved substances.
Solution:
On the basis of the concentrations and types of contaminants in these waste streams, the company decided to keep the streams separate to enable use of the best technical approach for their treatment and recovery of their contents.
This strategy also would provide the maximum recovery of rinse water (oily and non-oily) streams for recycling back to the manufacturing operations.
The first phase of the project was to characterize the various waste streams and establish the concentration of the primary contaminants. Based on the composition and concentration of each waste stream from the various manufacturing operations, they are segregated and piped to separate holding tanks for
- oily rinse-water streams,
- rinse-water streams,
- acid wastes, and
- base wastes.
The segregation of waste streams into these classifications allows for employing different waste-treatment-and-recovery equipment and systems in the design of the waste-treatment-and-recovery system.
Treatment Used
The largest volume of waste to be treated is the rinse water (oily and non-oily) stream. The oily rinse-water streams are pretreated to remove the immiscible oil phase and are then combined with all the other rinse water streams in an equalization tank.
The primary treatment for the rinse water streams is a combination of ultrafiltration (UF) and reverse osmosis (RO). The combination of these technologies recovers and recycles approximately 80% of the plant's total waste effluent. The filtrate from the UF and RO systems produces a clean water that is recycled back to the manufacturing operations.
The concentrated waste solutions--comprising UF-system concentrated waste, RO-system concentrated waste, neutralized acid waste, and neutralized base wastes--are combined and processed through a pretreatment system before discharge to the local POTW.
Results
This Fortune 500 manufacturer has successfully constructed a new manufacturing facility that meets--not only regulatory standards, but also--its own vision of a self-contained wastewater-treatment facility.
Contact: Mech-Chem Associates, Inc., 148 Main Street, PO Box 473 Norfolk, MA 02056. Tel: 508-528-5990; Fax: 508-528-8972; E-mail: info@mech-chem.com