Heat recovery adds to value of thermal oxidizer
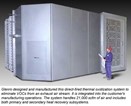
Oxidizers have become many manufacturers' method for meeting the challenges of increasingly stringent environmental controls on atmospheric release of VOC from their manufacturing processes.
A direct-fired recuperative thermal oxidizer, designed and manufactured by Glenro Inc., is being used to clean a manufacturing exhaust stream that contains organic hydrocarbon contaminants. The oxidizer system not only processes 21,000 scfm of exhaust but also uses primary and secondary heat recovery subsystems to recapture a large amount of heat energy for reuse in the process.
As with most thermal oxidizers, in the Glenro oxidizer, process exhaust is ducted to a combustion chamber, where a burner raises the air stream to a prescribed temperature. Contaminants burn to harmless products of combustion. Once the oxidizer reaches operating temperature, solvents in the exhaust stream ignite and begin to serve as a heat source for their own destruction. The more solvent present in the exhaust, the lower the oxidizer's fuel requirements.
As an added benefit, the new Glenro oxidizer includes primary and secondary heat recovery capability. The primary recovery subsystem preheats the oxidizer's inlet solvent-laden air stream before it goes to the combustion chamber, which results in significant energy savings. The secondary heat-recovery system, which includes an insulated air-mixing enclosure, merges a controlled portion of the clean, hot, oxidized exhaust air with room air to supply energy to a process oven. The remainder is used to fire a waste heat boiler that produces steam.
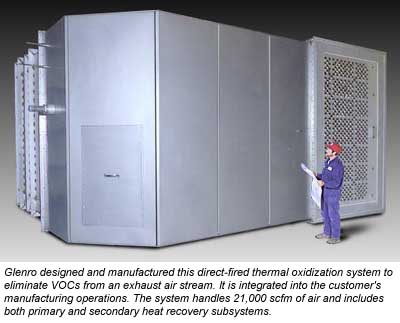
Four Recovery Units
The system's four heat-recovery units operate within the following operating parameters:
- Primary heat-recovery (exhaust preheat): 10,200,000 Btu/hr at an air flow
rate of 21,000 scfm - Secondary heat-recovery (oven process air): 12,500 scfm of air at 293ºF
- Secondary heat recovery (boiler/steam generator): 267 boiler hp
- Secondary heat recovery (plant make up air): 50,000 cfm at 75ºF
Heat recovered in the primary subsystem is used to preheat the incoming air before it goes into the oxidizer burner chamber.
The oxidizer is constructed of high-grade stainless steel and other heavy-duty materials for long service life.
The system was shipped pre-wired, pre-piped, and skid mounted for easy handling and installation. The system includes insulated ductwork.
Headquartered in Paterson, NJ, Glenro Inc. provides process-heating engineering and equipment for a wide range of industries and applications. Glenro serves customers through a nationwide network of sales offices.
Contact: Glenro Inc., Jim Alimena. Tel:1-888-453-6761.
Edited by Paul Hersch
Managing Editor, Pollution Online