Environmental cleanup of abandoned NY railroad yard enables development of intermodal facility
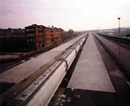
The cleanup of an abandoned railroad yard capitalizes on its location and helps an area of New York City steam toward a new life.
By Joseph J. Fiteni, Jr., P.E., Principal, TAMS Consultants, Inc., New York, NY
Establishing Priorities
Environmental Impacts
Intermodal Rail Operations
Additional Benefits
The 96-acre site of the former New York Central railroad yard, dormant for more than 20 years, has been transformed into the Harlem River Yard Intermodal Transportation and Distribution Center. The state-of-the-art multimodal park providing warehousing, distribution, and rail transportation services to businesses serving the New York City metropolitan region.
Located at the southern tip of the Bronx, the project is expected to contribute greatly to the revitalization of the area by bringing in new investment opportunities while providing access for containerized rail freight directly to the east side of the Hudson River for the first time in decades.
The Harlem River Yard was chosen in 1978 as the site for an intermodal facility to accommodate the metropolitan area's existing intermodal business and allow for the development of new services. Located at the edge of the Harlem River, which separates the Bronx from Manhattan, the site offers immediate access to water, rail, and highway facilities. It also serves as the southern landfall of the Oak Point Link "water route," a straight strip of rail that runs the length of the Bronx, from north to south along the Harlem River. The Oak Point Link was constructed to improve rail freight access to markets east of the Hudson River.
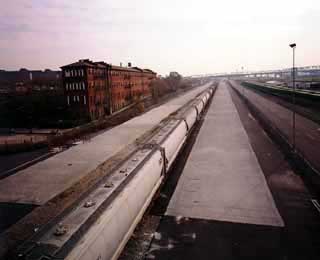
Adjacent to the site are two major highways -- the Major Deegan and Bruckner Expressways -- and three bridges that connect the site to New York City and Long Island. There is also an existing docking area at the southwestern section along the Harlem River. The site is zoned for heavy industry and is part of a larger industrial district that stretches in a wide band around the South Bronx waterfront from Hunts Point to Yankee Stadium. The location therefore builds upon established land use patterns and conforms with long-standing city and state policies to attract more manufacturing jobs to the area.
The plan to develop the site was structured to capitalize on the advantages of its location as well as the increased opportunities offered by changing technologies and new transportation network improvements. It also was devised as a response to the congested and costly truck movements in the region and efforts to improve ambient air quality standards.
In 1989, the New York State Department of Transportation (NYSDOT) selected Harlem River Yard Ventures Inc. (HRYV) as the developer of the project. HRYV retained TAMS to provide engineering and environmental services. Under a 99-year lease to develop the site, the NYSDOT required that the Harlem River Yard would be developed and operated as an intermodal transportation facility with a significant rail component to provide more efficient, and greater capacity freight transportation for the New York City/Long Island area. Priority markets to be served included refrigerated food and municipal solid waste.
The aims of the project, as defined the NYSDOT were to:
- Enhance the competitiveness of rail freight service in the New York City metropolitan area by developing an intermodal rail terminal in the Harlem River Yard, along with associated warehousing and infrastructure.
- Reduce truck traffic on Hudson River bridges.
- Reduce the cost of transporting materials into and out of New York City.
- Create jobs and offer an incentive to economic development.
TAMS's master plan called for an intermodal rail terminal that would serve as a terminal for the Oak Point Link. The terminal would include a secure unloading and container storage area capable of accommodating up to 100,000 containers or trailers annually. Among other land uses identified for the property were an intermodal solid waste transfer station and distribution warehouses. (Back to top)
Early in the project, several critical conceptual and design decisions were made with regard to environmental issues. Principally, it was determined that the environmental impact statement (EIS) required by the State Environmental Quality Review Act (SEQRA) would be performed as one comprehensive EIS using the worst-case scenario for the heaviest possible land use impacts. A tedious and painstaking effort in developing and analyzing a range of the most flexible future land-use options for the site resulted in a shovel-ready site with regard to review of environmental impacts, allowing tenants to break ground and proceed with development without having to perform further environmental analysis.
The EIS process typically takes from 12 to 14 months; the shovel-ready site was a time- and money-saving benefit for the owner, developer, and tenants. Separate tenant EISs would have taken almost two years each, a total of eight. The comprehensive EIS took only three years to complete and resulted in a cost savings of $750,000. It proved so effective that the procedure was adopted throughout New York State.
Once the master plan for the facility was approved, hazardous waste site assessments revealed the presence of abandoned underground tanks, lead and other metals, polyaromatic hydrocarbons (PAHs) related to coal and ash, and asbestos in abandoned on-site buildings. Much of the area was covered with varying depths of fill resulting from its past use as a rail yard and coal storage yard, which was the primary source of contamination. Coal particles were widely distributed throughout the site soils and were not amenable to physical separation. While semivolatile organic contaminants were present throughout the unsaturated overburden, there was no indication that the quality of groundwater was affected. This was determined through groundwater sampling and toxicity characteristic leaching procedure sampling.
In accordance with a remediation plan approved by the New York State Department of Environmental Conservation (NYSDEC), the entire brownfield site was covered with controlled fill or topsoil, or paved where appropriate for facility operations. Because the soil contaminants were not leaching into the groundwater, the control of airborne migration of contaminants was the primary remediation plan proposed. Materials or structures used as cover were those generally used in construction of the facilities, such as roadway and parking lot paving materials, building slabs, general fill, railroad bed materials, as well as topsoil for landscaping and lawn areas.
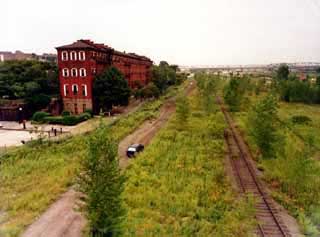
To preserve the effectiveness of these control measures, fill areas will be protected from erosion and other contaminants through a repaving plan that was part of the overall plan proposed to the NYSDOT by the owner. In addition, before the buildings could be demolished, the remediation plan entailed removing asbestos from the old railroad sheds, in accordance with New York City Department of Environmental Protection regulations, and disposing of the underground storage tanks.
The site also required the design of new drainage and utilities distribution systems. Existing on-site utilities were minimal and could not support new development. In anticipation of the widest variety of land uses, TAMS designed water, sanitary, drainage, electrical, and telecommunications distribution systems that would provide basic services to future tenants. A new site-wide drainage system was designed to direct future-use industrial wastewater into the city's sanitary sewage system and allow only uncontaminated stormwater to exit the site through outfalls directly into the Harlem River.
The benefit of this approach was that 13 existing and two proposed outfalls could be permitted through one umbrella NYSDEC State Pollution Discharge Elimination System Permit. Then, as individual tenants were approved for leased parcels, TAMS obtained individual NYC Department of Environmental Protection (NYCDEP) Connection and Industrial Waste permits for each leased property, saving the developer considerable expense. As a practical and aesthetic consideration, all electrical lines were buried. (Back to top)
The centerpiece of the Harlem River Yard is the intermodal rail terminal. It occupies the largest section on the site, approximately 28 acres along the northern section. The terminal is designed to function as either a container on flatcar or trailer on flatcar facility. Goods arriving via rail are transferred to trucks for distribution to the New York City area. Goods arriving via truck are transferred to rail cars for transport to regional end-users.
Railroad service is provided to and from the Harlem River Yard by CSXT, formerly Conrail, and it is anticipated that additional service by a second rail provider will begin in the near future. Recent improvements to the rail lines in the Bronx and along the Hudson River, allow, for the first time, piggy-back freight cars, which carry complete truck trailers, to come directly into the city. Because of the limited windows available for receipt and delivery of trains through the Bronx, the site plan provided long forwarding and receiving tracks so that the over-the-road locomotives can be turned around quickly. Yard locomotives break up and assemble trains and shunt strings of cars between working sidings and forwarding/receiving tracks.
The intermodal terminal has 5,250 linear feet of rail adjacent to paved roadways for loading and unloading trains. Intermodal trains up to 128 cars long are loaded or unloaded, and one daily train of 128 platforms apiece can be handled using the proposed yard trackage at the Harlem River Yard. Thus the total intermodal service to the Bronx could approach 100,000 trailer loads a year. When trains enter the yard, large forklift trucks lift the trailers off and deposit them in a parking lot where they can meet up with a tractor for local delivery. Computerized management systems are used in the terminal to optimize space utilization, loading sequence, and pre-blocking.
Site roadways and a rail track configuration were designed to accommodate both the anticipated intermodal operations and future tenant development of lease properties. The road/track configuration can handle most surface transportation activities completely on site. Also, while typical highway pavement grade would be classified for HS20 loading, TAMS's specifications for all roadways within the Harlem River intermodal facility call for heavier duty HS25 loading that would wear well under the weight of an exceptionally large number of heavily loaded vehicles. (Back to top)
The development of the Harlem River Yards offers numerous benefits to the public as well as savings to the state. Some of them derive from a new 11-acre intermodal truck-to-rail, solid waste transfer station that is in operation on the site. The new station allowed the closure of three old, substandard city waste transfer facilities and the reduction of processed volume in a fourth, eliminating standing sanitation-truck traffic in three of the neighborhoods and eliminating it entirely in the fourth. Another 16-acre part of the site is the new home of the New York Post printing plant. The selection of the site at the Harlem River Yard will facilitate the shipment by rail of the large volume of newsprint required by the New York Post.
From the public perspective, the Harlem River Yard project brings with it a major infusion of capital, new businesses, and a wide variety of job opportunities. It also produces significant savings in transportation costs and consequent reductions in the final prices of numerous products, which make local businesses more competitive. The completion of the project will ultimately result in an estimated 800 to 1,000 new jobs, predominantly blue collar, transportation, and warehousing jobs, a labor market that is particularly needed in the area. It is expected that the continued operation of the facility will create a demand for numerous support services and spinoff businesses, such as truck repair and food and lodging facilities that would benefit from proximity to the transportation complex. There are many vacant sites and under-utilized buildings in the manufacturing district adjacent to the facility that can accommodate such businesses.
The decrease in vehicle miles of travel by trucks is expected to be 3.4 million miles a year, based on a decrease of 680,000 truck trips a year with an average haul length of five miles in New York City. The reduction in travel of high-emission vehicles results in the annual cutting of pollutants by 310 tons of carbon monoxide, 30 tons of hydrocarbons, and 20 tons of nitrogen oxides.
By increasing the proportion of goods shipped in and out of New York City by rail, traffic congestion is alleviated on trans-Hudson crossings, particularly on the George Washington Bridge. Round trip truck movements on Hudson River crossings will be reduced by about 340,000, which is equivalent to approximately four percent of total truck traffic on the six crossings operated by the Port Authority of New York and New Jersey.
The site of the contaminated abandoned railroad yard is now a viable industrial center. Still in its infancy, the Harlem River Yard has already helped to revitalize a depressed section of the city, enhanced rail service, reduced truck traffic and air pollution, and cut the cost of transporting materials in and out of New York City. (Back to top)
About the author: Joseph J. Fiteni Jr., P.E., is a Principal, TAMS Consultants Inc., New York, NY. (Back)