Earth-Friendly Parking Lots Now A Reality With TrueGrid Permeable Pavement
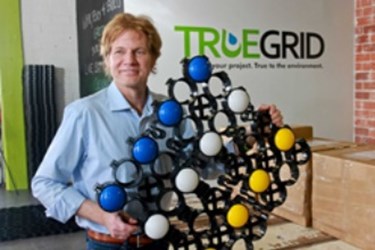
Barry Stile's invention of TRUEGRID, a new type of permeable pavement that is 98% permeable and made up of 90% recycled polymer materials. TRUEGRID is beneficial to the environment because it allows stormwater runoff to penetrate the ground rather than run across the surface as with pervious pavements thus risking the pollution of groundwater supply and local ecosystems.
Houston, TX (PRWEB) - New pavement solution made of 100-percent post-consumer recycled content reduces runoff, protects groundwater.
Houston-based toy inventor Barry Stiles is the creative mind behind a new type of permeable pavement -- one that significantly raises the bar for parking lots everywhere.
Traditionally paved parking spaces are sites of major stormwater runoff. Because water cannot penetrate pervious pavements like asphalt and concrete, it instead runs across the surface, ultimately posing a danger to the quality of groundwater supplies and local ecosystems. However, parking lots can be made significantly eco-friendlier with the installation of TrueGrid, a plastic paving system that is 98 percent permeable -- thus allowing water to absorb directly into the ground rather than running off the surface of the pavement.
TrueGrid is comprised of plastic grids that fit together to cover as large a surface as necessary. The grids themselves are composed of circular cells, capable of bearing up to 6800 psi -- and that’s before the circles are filled with strengthening materials such as crushed shale, gravel or even grass. The result is a flat surface that can support the weight of cars and even big rigs.
The paving system has a number of other potential benefits and applications for businesses and public areas.
Permeable pavement may help businesses use space more efficiently, eliminating the need for detention ponds, which are temporary retention structures that collect stormwater and allow it to evaporate between storms.
"One of the unique features of our product is that you can put your detention underneath the parking lot, so you have a usable surface," Stiles told the Houston Chronicle in March. "Instead of wasting land with an ugly concrete detention pond that only breeds mosquitoes."
In addition, the drainage prevents flooding, which can damage property and cause erosion. It also allows for bioremediation, which uses living organisms to clean runoff and break down harmful toxins before they can enter the water supply.
By draining quickly and retaining more water than other types of pavement, TrueGrid also creates a cleaner, drier parking area for customers. Moreover, the use of porous pavement substantially reduces the "heat island effect" common in parking lots on other impervious paved structures.
Another of TrueGrid’s potential benefits is that it requires little or no maintenance over the 40-year life cycle of the product. (The exact life expectancy ranges between 25 and 60 years.) It also does not shrink and expand with the changing of seasons as asphalt and concrete do, so it doesn't require periodic patching -- nor does it break when the soil beneath it goes through seasonal changes. This is due to its unique flex-joint technology, which allows the grids to move along with the earth beneath.
Unlike those covered in porous asphalt or concrete pavement, TrueGrid-paved surfaces do not need to be cleaned out periodically. Sediment that gets deposited on top of TrueGrid permeable pavement simple washes into the ground below and does not prevent future stormwater from draining.
TrueGrid pavement also has the potential to transform parking lots from paved blacktop to greenspace. If customers do not need the extra load-bearing capacity of gravel, they can instead fill the grid with grass or other low-growing, traffic-tolerant plants.
Available along with the paving system are snap-in “SuperSpots,” which pop into the circular spaces to designate parking areas. Various colors are available, including white, blue and yellow.
A TrueGrid installation generally costs 10% to 50 % less than a concrete installation on a square foot basis, depending on site preparation. The ability to utilize land to generate revenue for years to come, or purchase less land in the first place, presents a huge financial upside compared to building and maintaining an expensive detention pond.
Stiles, who earned a degree in plastics engineering from the University of Massachusetts, explained to the Chronicle that he got the idea for the paving system in Germany six years ago, where high population density requires this type of innovation. He felt sure he could create something even better back home -- so he did.
The TrueGrid paver has a full utility patent.Stiles already has several takers. Among his clients are the Whole Foods Market, Stripes Convenience Stores chain, the Saint Arnold Brewing Co, Walter Reed Army Medical Center and Pocono Raceway.
Source: PRWeb
View original release here: http://www.prweb.com/releases/2015/04/prweb12650794.htm