Anguil Controls VOC Emissions from Asian PTA Plant
Treating PTA plant emissions requires a thorough knowledge of the plant's process streams, seamless integration of control devices into the existing process, and extensive experience with oxidation technologies.
A recent VOC control project for a PTA plant in Asia explains the technology selection and design considerations of Anguil Environmental Systems, Inc.
Process and Technology Selection
PTA plants typically generate a high volume of process emissions, in the range of 32,000 to 95,000 scfm (50,000 to 150,000 nominal m3/h). The Asian PTA plant where the VOC control system was installed averages 12-million Btu/h of gas flow. The main emissions are carbon monoxide, methyl bromide, and various organic compounds. The high-pressure exhausts from the PTA primary absorbers pass through an expander that reduces the pressure to 4 psig. This subsequently is reduced to between 1 to 2 psig through a pressure-reduction valve.
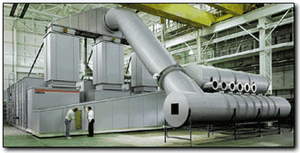
To deal with the high loading of CO and the presence of methyl bromide (about 0.005 vol%), Anguil selected a catalytic recuperative oxidation system. The catalytic system uses a special platinum/palladium-based catalyst designed by the Johnson Matthey Catalytic Systems Division for PTA plant exhausts. The catalytic recuperative oxidizer operates at 350 ºF to oxidize CO and methyl bromide. The low oxidation temperature of the catalytic oxidizer results in savings on fuel and operating costs.
The catalyst oxidizes the methyl bromide to hydrogen bromide (HBr). A steam preheater on the shell side of the heat exchanger prevents the HBr from dropping below the dew point and corroding the equipment (fabricated from Type 316L stainless steel).
Varied Organic Loading
The process exhaust from the PTA plant varies in organic loading, and the catalytic oxidizer design must accommodate these varying levels with minimal use of auxiliary fuel. The system handles the changing levels of organic loading by using a bypass on the 316L stainless-steel shell-and-tube heat exchanger.
According to low organic-loading conditions, the heat-exchanger bypass is closed so that the full effectiveness of the heat exchanger is available to preheat the incoming stream. At high organic loading, the outlet temperature of the catalyst is raised, resulting in a high preheat temperature from the heat exchanger. The high preheat temperature, however, could cause overheating and shutdown of the system. To prevent overheating, Anguil supplied a "hot side" heat exchanger bypass that controls the preheat temperature from the heat exchanger.
Catalyst Selection
The selection of proper catalyst to oxidize both the carbon monoxide and the methyl bromide at low temperatures was another critical aspect of the project. Historically, halogenated compounds have had damaging effects on both noble-metal and base-metal oxidation catalysts. However, there have been several significant recent advances in catalyst technology, including the platinum/palladium-based Halocat ™ catalyst deposited on a ceramic substrate used in this design.
Anguil's proprietary catalyst rack design, including specialty "gasketing," eliminated the risk of gas bypassing the catalyst and subsequent incomplete destruction.
Postscript
The Anguil catalytic recuperative oxidation system went online in early 1999 and is currently operating and achieving the regulatory compliance demanded of the PTA plant. Operating costs are minimized because essentially no auxiliary fuel is needed. Based on the success of the system, the customer purchased an identical 90,000-scfm unit. Anguil has installed similar systems for PTA manufacturers in the Middle East and the southeastern U.S.
Anguil Environmental Systems provides air pollution control solutions worldwide. Specializing in VOC, HAP and NOx control and abatement, Anguil's engineering expertise and 20+ years of experience allow it to custom-design cost-effective, trouble-free, compliant air-pollution-control systems.
For more information about this technology, contact: Chris Anguil, Anguil Environmental Systems, Inc. 8855 North 55th Street, Milwaukee, WI 53223 Tel: 414-365-6400 Fax: 414-365-6410; E-mail: info@anguil.com
The previous case study was rewritten by Chris Anguil from a feature article edited by Nick Basta for Chemical Online, which is a sister site to Pollution Online within the VerticalNet family.