Air-pollution-control Methods--Part 3: More Equipment Types
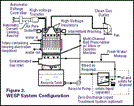
A venturi scrubber with pressure drop 12.25 in. water column performs with an efficiency of 50% for particles of less than 1 micron and 98% for particles larger than 2 microns. By comparison, the wet electrostatic precipitator delivers 99% efficiency--and more--regardless of particle size.
Moving on up from the equipment discussion begun in the last installment, this final leg of a three-part series establishes the stable platform for choosing among the family of air-pollution control devices. Covered here are the several types of electrostatic precipitators available, including their principles of operation and performance
Electrostatic Precipitators
Electrostatic precipitators (ESPs) are particularly effective at removing particles of less than 1 micron, since they typically respond well to electrical forces. The electric force on a 0.1-micron electrically charged particle can be more than a million times that of the force of gravity.
Because an ESP uses electricity only to charge the particles in an air stream and not influence the air stream itself, its energy consumption is much less than for a Venturi scrubber, which must move the entire gas stream through a Venturi throat.
Electrostatic precipitators are of many types and configurations, but all depend on separating suspended particles from a gas stream during three fundamental steps:
1. Electrically charging suspended particles by gaseous ions produced by corona discharge
2. Collecting the charged particles on electrodes
3. Removing material from the collecting electrodes to a storage area located inside or outside of the ESP.
In a dry ESP, the electrodes are periodically shaken to remove accumulated particles for disposal. However, dry ESPs are prone to buildup on the walls of the collection chamber; which acts as an electrical insulator, reducing performance and efficiency. If the hospital incinerator's exhaust stream contains VOCs and acid gases, the dry ESP must be used in concert with scrubbers or other equipment.
In a wet ESP (WESP), a liquid, usually water, continuously washes particulate buildup away from the collection surface. The WESP finds wide use in applications where the gas to be treated is hot, has a high moisture content, contains "sticky" particles, has been pretreated in a scrubber but requires additional removal. However, the stream still holds particulate and acid droplets, or contains sub-micron particles not amenable to treatment through other methods.
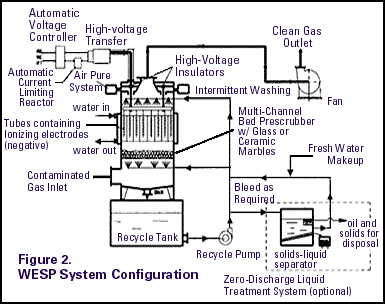
WESPs are of three varieties. upflow, downflow, and condensing.
In a conventional, upflow WESP, the gas stream flows co-currently to the water. This type requires frequent cleaning (periodic shutdown) because many droplets from the bottom water sprays do not reach the top of the collecting chamber where sub-micron particles accumulate. Also sprayers are susceptible to plugging from solids in the recycled water.
In a conventional WESP, such as one used with the incineration system in Figure 2, the hot, contaminated inlet stream is cooled from 500º to 140ºF in a quencher before large particles are removed in a low-energy scrubber. The pre-treated gas stream passes into a series of tubes with ionizing electrodes at their centers. Each electrode has a number of sharp points, which effects a corona discharge that "mobilizes" the particles. When the particles reach their saturation charge, they migrate toward the walls of the collecting tubes.
In a downflow WESP, the inlet gas and water sprays move counter-currently downward. This mostly overcomes the spray limitations inherent to the co-current design. However the design has a problem with mist elimination.
The condensing WESP increases removal efficiency and reduces operating costs and maintenance by harnessing thermodynamics to effect particle movement perpendicular to the gas flow direction. This design combines a heat exchanger (which cools the gas stream) into an upflow, vertical tube WESP. The unit thus can contend with the variables of velocity, particle size, and temperature to maximize the removal of sub-micron particles.
In a condensing WESP, charged particles (both liquid droplets and solids) are subject to electrical forces, as well as thermophoresis and diffusiophoresis.
The device's double-walled collection chamber internally circulates cold water in a closed-loop system. When a gas-temperature profile exists on either side of a particle, the gas molecules on the warmer side have a greater kinetic energy than the molecules on the cooler side. This kinetic differential forces the particle toward the cooler temperature zone (a process known as thermophoresis).
Particle velocity depends on the temperature gradient, the relative thermal conductivity of the gas and the particle, and the density and viscosity of the gas. Thermal forces on particles of 0.1 micron can be 100 times those for particles of 1 micron.
Diffusiophoresis, occurs when the partial vapor pressure of water in a carrier gas is greater than the water vapor pressure at the surface of the water droplets in a scrubbing liquid. Here, water vapor will condense onto the water droplets, creating a bulk motion of gas and entrained particles toward the droplets. Because the droplets are larger than the particles, and thus more easily removed by either electrical or mechanical means, diffusiophoresis can have a significant additional effect upon the electrostatic efficiency of collecting fine particles.
In a condensing WESP, charged particles (both liquid droplets and solids) migrate toward the positive (grounded) wall of the collection tubes. These tubes are cooled by circulating water. Water vapor condenses and leaves a wet film on the wall, which flushes particulate down the wall and out of the system. The wet film on the collection surface of the WESP keeps equipment running in a continuously self-cleaning mode.
By condensing water vapor from the contaminated gas, this WESP design can cut external water needs by 30% compared with a conventional WESP. The continuous presence of condensate on the surface of the collecting tubes also reduces corrosion .
The power level and efficiency of a WESP can be dramatically increased by careful design of the automatic voltage control system. While the industry average seldom exceeds 40% conduction, systems can be designed to deliver 86% conduction (the theoretical maximum) to a corona discharge (Figure 3).
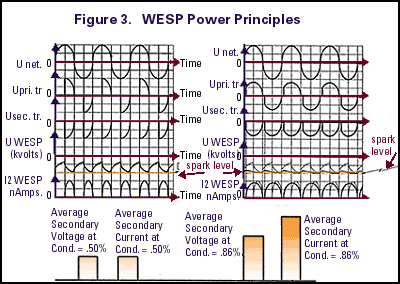
The combination of liquid scrubbing, thermophoretic and diffusiophoretic effects, and high-voltage electrostatic precipitation in a condensing WESP is an effective way to remove sub-micron particles from a hospital incinerator gas stream. The equipment produces zero opacity, satisfying state and federal regulations for incinerator exhaust. Combined with a relatively inexpensive, low-energy scrubbing section which acts as the air distribution device, both large and very small particles (down to 0.01 micron) can be removed from the exhaust with minimum maintenance.
Applying Lessons Learned
Table 4 enables the matching of process requirements and available technologies to fulfill best available control technology (BACT) for medical and biological waste incineration. The table also illustrates how well the collection categories are satisfied by wet electrostatic precipitators. These are an excellent match with the requirements for air pollution control of incinerated hospital waste.
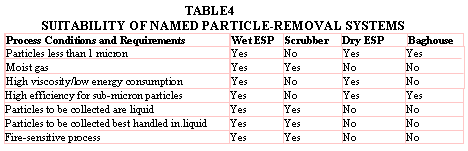
Air pollution control devices--particularly those for the removal of sub-micrometer particles--should be able to operate as part of an integrated system. For example, by combining a WESP with a relatively inexpensive, low-energy scrubbing section (which acts as the air-distribution device), large and small particles (down to 0.01 micron) can be readily removed from exhaust with minimum maintenance.
About the author: Isaac Ray is vice-president of Research and Development for Croll-Reynolds Clean Air Technologies, Westfield, NJ 07091. He holds an MS in mechanical engineering from Lomonosoff Technological Institute (Ukraine) and a Ph.D. in mechanical engineering from the Civil Engineering Institute(Ukraine). He has more than 30 years' experience designing and building air-pollution-control systems in the Soviet Union and U.S. He is regarded among the leading experts in wet electrostatic precipitation technology. Ray holds the Gold Medal for Innovation in Industry from the former Soviet Union. He can be contacted via Tel: 908-232-4200; E-mail iray@croll.com; Fax: 908-232-2146.