Air-pollution-control Methods--Part 2: Equipment Types
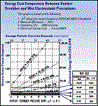
Having covered the basics of incinerating waste in part 1, we turn here to discuss some of the principal devices for removing particles from the incinerator's emissions--since the particles in a gas stream have no chance to settle.
The gas stream carries the particles along to the collection device, which may be a bag house, a wet scrubber, or some appliance exerting an electrical force (such as an electrostatic precipitator).
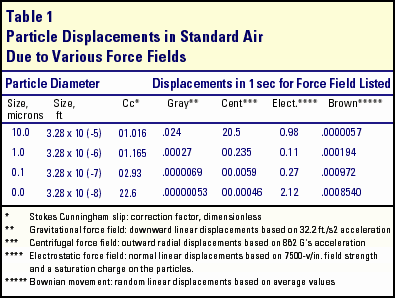
Fundamentals of Particulate Control Equipment
A number of collection methods are available to control the gaseous discharge from a hospital-waste incinerator. In ascending order of efficiency and relative cost effectiveness, they are fiber filters; scrubbers; and dry, wet, and condensing wet-electrostatic precipitators.
Fiber filters. These work best for an exhaust containing only liquid mist.
The fiber filter, also known as the fiber-bed mist eliminator, consists of glass or polyester fibers of five to 10 microns diameter packed between flat or concentric screens.
The efficiency of mist removal by the fiber filter increases commensurately with the density of the packing and thickness of the fiber bed. However, the pressure drop through the bed and probability of plugging also rise.
Mist and submicron particles collect on the surface of the fibers by several mechanisms:
- Particles larger than three microns usually collect by inertial impact since their size prevents them from flowing through.
- Particles of one micron and less experience direct interception as they contact the fibers.
- Fine particles, smaller than 0.1 micron, because they exhibit Brownian diffusion--that is, random movement--in addition to their flow velocity, collide with gas molecules, increasing the probability of their colliding with droplets of mist and the fibers of the bed.
Brownian diffusion is the paramount collection mechanism for one-micron smoke particles from incinerators.
Design drawbacks. Fiber-bed filters usually are packed manually, so the quality of packing is difficult to control.
The pressure drop in fiber-bed filters can be as high as 15-in. water column (wc) due to the filter's small-diameter fibers and dense packing. For a typical exhaust of 20,000 scfm at 320ºF, the exhaust blower requires a costly 100-hp motor.
The face velocity for a 99% efficient filter is 40 fpm, which requires 500 sq. ft. of face area for the typical exhaust flow, or a minimum of eight cylindrically shaped 24-in. diameter filters, 120 ft long.
In addition, a clogged filter is classified as toxic waste; so disposal and replacement of filter elements can cost $40,000 a year. A cooling section may also be required.
Combined installed capital-equipment and operating costs can be very high.
Wet scrubbers. The first patent for a particulate-control scrubber was issued in 1901.
As do fiber filters, wet scrubbers rely on impaction, interception, and diffusion to separate particulates from the gas stream, with liquid droplets taking the fibers' filtering role.
The scrubbing liquid usually is water mixed with precipitated particles and absorbed gases. Droplets are deliberately generated in the scrubber as targets for particles. Unlike the situation for the particles, the droplets, being larger and heavier, can be removed by inexpensive mechanical devices such as cyclonic separators.
For hospital-incinerator exhaust, wet scrubbers can successfully and readily remove lint particles, usually above five microns. However, most of the contaminants in the incinerator exhaust are smaller than one micron. To remove them successfully, the target droplets need to be about 10 to 15 microns in diameter. Substantial electric power is required to generate these droplets in quantities ensuring good scrubbing efficiency.
The most popular type of wet scrubber for submicron particulate removal is the high-energy venturi scrubber (HEVS). This scrubber is essentially a gas-atomizing device that relies on shear and impact to break water into fine droplets. The design goal is to produce an evenly distributed cloud of fine droplets at high density providing the high target efficiency--or probability of a collision--between submicron droplets of condensed heavy metals and the much larger droplets of recycling liquid.
The droplets are produced in the venturi throat, where velocity of the moving gas can be as high as 400 fps, eight times more than the velocity of the exhaust gas in the duct. Since pressure drop is proportional to the second power of the gas velocity, actual pressure losses are 64 times higher then in the duct delivering the gas.
Figure 1 demonstrates the relationship between particle size to be captured, pressure drop in the venturi throat, and corresponding energy requirements.
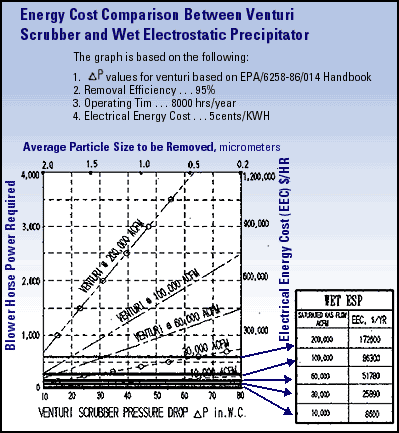
The scrubber should be capable of removing large and small particulates without clogging, while providing adequate surface area for the interaction of gas and liquid. Applicable scrubbers for medical-waste incineration include:
- Multi-rod deck, where gas and scrubbing liquid compete for the space between solid tubular structures and intermixing occurs in a very turbulent fashion.
- Multi-channel, where channels are created by solid glass or ceramic spheres called "marbles." When contaminated gas and scrubbing liquid enter the space between the rotating marbles, the scrubbing includes not only absorbed gas, but also solid particles that are trapped in the scrubbing liquid. Efficiency of removal for the particles above two microns can be better than 90%. Also the possibility exists for substantial odor reduction due to the mass-transfer capability of the marbles flooded with scrubbing liquid.
For incinerator exhausts contaminated with solid particles and liquid mist, the optimum scrubbing system involves hot gas' at 500º to 600ºF entering a low-pressure-drop scrubber-quencher.
The gas cools to full saturation temperature while large particles of ash are trapped in the scrubbing liquid. The vapors of heavy metals that condense in the quencher become submicron particles. These particles, together with large droplets of scrubbing liquid, enter a separation chamber where gravity or centrifugal action separates the large particles of liquid and solids from the gas.
Efficiency of separation depends on the design. Since fine particles generally do not respond well to gravitational force, settling chambers are not typically effective.
Cyclonic separators, which rely on centrifugal force, are preferred. The cyclonic separator's centrifugal force is directly proportional to both particle mass and tangential velocity to the second power and inversely proportional to the radius of the turn.
The inlet velocity required for separating fine particles may result in excessive energy consumption and wear on the equipment. This makes centrifugal separators impractical for the removal of submicron particles, but they can be useful adjuncts to other equipment.
About the author: Isaac Ray is vice-president of Research and Development for Croll-Reynolds Clean Air Technologies, Westfield, NJ 07091. He holds an MS in mechanical engineering from Lomonosoff Technological Institute (Ukraine) and a Ph.D. in mechanical engineering from the Civil Engineering Institute(Ukraine). He has more than 30 years' experience designing and building air-pollution-control systems in the Soviet Union and U.S. He is regarded among the leading experts in wet electrostatic precipitation technology. Ray holds the Gold Medal for Innovation in Industry from the former Soviet Union. He can be contacted via Tel: 908-232-4200; E-mail iray@croll.com; Fax: 908-232-2146.